
About Link drive Eccentric press LS 4 model
1. Drive and Control Systems
The LS 4 model features a multi-link drive with options for six or eight links, designed using specialized software for precise performance. It combines an asynchronous drive to minimize lateral forces and a high-speed herringbone gear drive for smooth operation. The machine also offers dual control options—electronic cam and mechanical cam—providing flexibility and precision in operation.
2. Structural and Safety Enhancements
Key components are optimized using Finite Element Method (FEM) analysis for strength and durability. The slide is guided by an eight-sided rectangular guide for stability and accuracy. Safety features include a pneumatic friction clutch brake with an optional imported wet type clutch brake, as well as a hydraulic overload protector to ensure reliable operation.
3. Lubrication and Optional Features
The main lubrication is automated with oil, and an optional heating and cooling system helps maintain optimal operating temperatures. Additional options include an air cushion for improved surface finish and a quick die change device to enhance productivity.

Composition of Equipment
System Architecture
The Link Drive Eccentric Press LS 4 is composed of a precision-engineered multi-link drive, which can be configured with either six or eight links to meet specific operational requirements. The drive system is meticulously designed using advanced software to ensure optimal performance and efficiency.
Component Enhancement
Critical components of the press are enhanced through Finite Element Method (FEM) analysis, ensuring maximum durability and reliability. The slide is guided by an eight-sided rectangular guide, providing exceptional stability and precision during movement.
Operational Dynamics
The press integrates dual control systems—electronic cam and mechanical cam—to offer flexible and precise control over operations. It features a pneumatic friction clutch brake with an optional imported wet type clutch brake for partial rotation control, along with a hydraulic overload protector to prevent damage from excessive forces.
Support Systems
The main lubrication is automated with oil to ensure smooth and consistent operation. The press also offers optional features such as a heating and cooling system, an air cushion for improved surface finish, and a quick die change device to boost productivity.
Working Principle

The multi-link drive system converts rotational motion into linear pressing force through interconnected links.

An asynchronous drive mechanism minimizes lateral forces during the sliding motion, ensuring precise and stable operation.

Dual control systems—electronic and mechanical cams—provide flexible and programmable motion control to adapt to various production requirements.

Main Advantages
High Precision and Stability
The multi-link drive system and eight-sided rectangular slide guide ensure precise and stable movement, minimizing misalignment and improving part quality.
Versatile Control Options
Dual control systems (electronic and mechanical cams) provide flexibility, allowing operators to choose the most suitable control mode for different production tasks.
Advanced Lubrication and Thermal Management
Automatic oil lubrication and optional heating/cooling systems maintain optimal operating conditions, extending component life and reducing maintenance.
Efficient Force Management
The asynchronous drive minimizes lateral forces during operation, reducing wear and tear on components and enhancing overall efficiency.
Enhanced Safety and Reliability
Features such as the hydraulic overload protector and optional wet type clutch brake safeguard the machine from damage and ensure reliable operation.
Productivity Enhancements
Optional features like the quick die change device and air cushion improve production efficiency and reduce downtime, making the press highly adaptable to various manufacturing needs.
Capacity
LS4-800
Nominal force: 8000 kN
Nominal stroke: 13 mm
Slide stroke: 900/1000 mm
SPM (Strokes Per Minute): min-1 to 10-18
Max. die height: 1200 mm
Die height adjustment: 500/600 mm
Bolster (F-B×L-R): 2200×4000 mm
Slide area (F-B×L-R): 2200×4000 mm
Main motor power: 200 kW
Direction of moving bolster: L-R, F-B, LT/RT
LS4-1000
Nominal force: 10000 kN
Nominal stroke: 13 mm
Slide stroke: 900/1000 mm
SPM: 10-18
Max. die height: 1200 mm
Die height adjustment: 500/600 mm
Bolster (F-B×L-R): 2200×4000 mm
Slide area (F-B×L-R): 2200×4000 mm
Main motor power: 200 kW
LS4-1250
Nominal force: 12500 kN
Nominal stroke: 13 mm
Slide stroke: 900/1000 mm
SPM: 10-18
Max. die height: 1200 mm
Die height adjustment: 500/600 mm
Bolster (F-B×L-R): 2200×4200 mm
Slide area (F-B×L-R): 2200×4200 mm
Main motor power: 250 kW
LS4-1300
Nominal force: 13000 kN
Nominal stroke: 13 mm
Slide stroke: 900/1000 mm
SPM: 10-18
Max. die height: 1200 mm
Die height adjustment: 500/600 mm
Bolster (F-B×L-R): 2200×4200 mm
Slide area (F-B×L-R): 2200×4200 mm
Main motor power: 250 kW
LS4-1600
Nominal force: 16000 kN
Nominal stroke: 13 mm
Slide stroke: 1200/1400 mm
SPM: min-1 to 10-18/16
Max. die height: 1400 mm
Die height adjustment: 600/700 mm
Bolster (F-B×L-R): 2500×4500 mm
Slide area (F-B×L-R): 2500×4500 mm
Main motor power: 280 kW
LS4-1800
Nominal force: 18000 kN
Nominal stroke: 13 mm
Slide stroke: 1200/1400 mm
SPM: 10-18/16
Max. die height: 1400 mm
Die height adjustment: 600/700 mm
Bolster (F-B×L-R): 2500×4500 mm
Slide area (F-B×L-R): 2500×4500 mm
Main motor power: 350 kW
LS4-2000
Nominal force: 20000 kN
Nominal stroke: 13 mm
Slide stroke: 1200/1400 mm
SPM: 10-18/16
Max. die height: 1400 mm
Die height adjustment: 600/700 mm
Bolster (F-B×L-R): 2500×4500 mm
Slide area (F-B×L-R): 2500×4500 mm
Main motor power: 400 kW
LS4-2400
Nominal force: 24000 kN
Nominal stroke: 13 mm
Slide stroke: 1200/1400 mm
SPM: 10-18/16
Max. die height: 1500 mm
Die height adjustment: 600/700 mm
Bolster (F-B×L-R): 2600×5000 mm
Slide area (F-B×L-R): 2600×5000 mm
Main motor power: 450 kW
LS4-2500
Nominal force: 25000 kN
Nominal stroke: 13 mm
Slide stroke: 1200/1400 mm
SPM: 10-18/16
Max. die height: 1500 mm
Die height adjustment: 600/700 mm
Bolster (F-B×L-R): 2600×5000 mm
Slide area (F-B×L-R): 2600×5000 mm
Main motor power: 450 kW
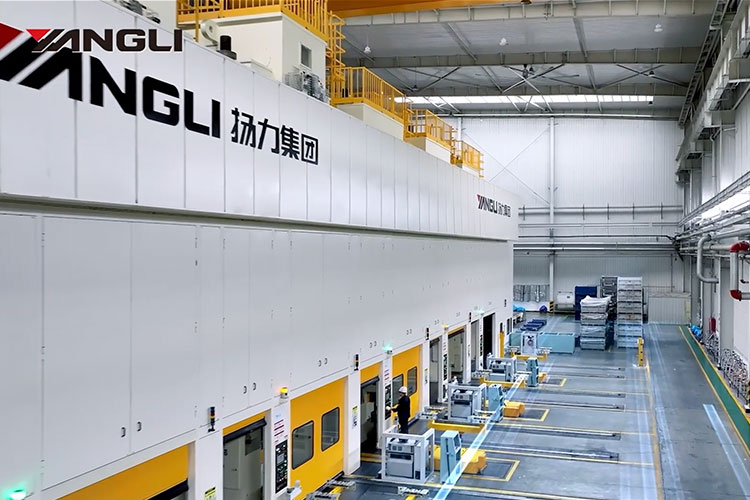
