
Description of mechanical presses
Our mechanical presses are high-efficiency and precision equipment for industrial production, integrating advanced technology and high-quality materials to provide reliable press processing solutions for various manufacturing industries. The product range includes:
C-Frame Gap Frame Crank Press
H-Frame Gantry Frame Crank Press
Straight Side Tie-rod Frame Press
Straight Side Tie-rod Frame Press
Servo Press
Composition of equipment
Drive System
The drive system uses high-strength components such as gears and crankshafts to ensure stable and efficient power transmission. Some models are equipped with advanced servo motor drive systems for precise control.
Machine Structure
Available in C-frame, H-frame, and straight-side configurations, the frame is welded from high-quality steel and treated for aging, offering excellent rigidity and stability.
Control System
The intelligent control system allows for precise parameter setting and adjustment, with fault diagnosis and warning functions to ensure stable operation of the equipment.
Auxiliary Devices
Including lubrication systems, cooling systems, and safety protection devices, these enhance the reliability and service life of the equipment while ensuring the safety of operators.
Working principle
Main advantages
High Efficiency
Some high-speed models of presses can achieve a high number of strokes per minute. Combined with automated loading and unloading systems, this significantly boosts production efficiency.
Precision
Equipped with high-precision guiding systems, drive components, and advanced control systems, the press ensures accuracy in ram motion and repeatability, enabling precise processing.
Stability
The high-quality machine structure design and manufacturing process, along with reliable drive and control systems, ensure stable operation under long-term, high-load conditions.
Flexibility
Models like the Servo Press can freely adjust the ram motion curve and processing parameters according to different process requirements, meeting diverse production needs.
Low Maintenance
Optimized structural design and the use of high-quality components reduce maintenance points and workload. Additionally, an intelligent fault diagnosis system is equipped for quick troubleshooting and resolution.
Product types
C-Frame (Gap) Crank Press:
This type of press features a compact and open C-frame structure, offering excellent accessibility to the workpiece. It is ideal for applications that require moderate press force and quick, high-efficiency stamping. Commonly used in industries such as automotive, electronics, and general manufacturing.
Main Technical Parameters:
Nominal Force: 160-4000kN
Stroke Length: 2-10mm
Strokes per Minute: 25-135min-1
Optional Configurations:
Automatic Feeding System
Air Cushion
Speed Available
H-Frame (Gantry) Crank Press:
Similar to the C-Frame (Gap) Crank Press, the H-frame (Gantry) design features a more robust and rigid structure, offering greater stability and higher force capacity. This type is ideal for heavy-duty operations and applications requiring larger working areas.
Main Technical Parameters:
Nominal Force: 1100-11000kN
Stroke Length: 3-650mm
Strokes per Minute: 8-70min-1
Optional Configurations:
Automatic Feeding System
Air Cushion
Speed Available
Straight Side Tie-Rod Frame Press:
The straight side tie-rod frame press is known for its high precision and rigidity, making it suitable for industries that demand high-performance, such as aerospace, automotive, and metalworking. Its straight side frame design ensures uniform pressure distribution, reducing deflection during operation.
Main Technical Parameters:
Nominal Force: 2500-36000kN
Stroke Length: 6.5-13mm
Strokes per Minute: 10-60min-1
Key Features:
High Precision and Rigidity
Suitable for Precision Manufacturing
Enhanced Frame Design for Stability
Forging Press:
This type of press is specifically designed for forging processes, capable of delivering high force and energy output to shape metal materials under extreme conditions. Commonly used in the forging industry for creating parts such as automotive components, aerospace parts, and heavy machinery.
Main Technical Parameters:
Nominal Force: 1500-40000kN
Stroke Length: 4-30mm
Energy Output: 18.5-1500kW
Applications:
Metal Forging
High-Temperature Shaping
Heavy-Duty Operations
High-Speed Press:
High-speed presses are designed for rapid and efficient stamping, offering a high number of strokes per minute to increase production output. They are ideal for industries requiring fast-paced production with high-volume, precision stamping.
Main Technical Parameters:
Nominal Force: 160-3150kN
Stroke Length: 1.5-10mm
Strokes per Minute: 20-1000min-1
Advantages:
High-Speed Stamping
Increased Production Efficiency
Suitable for High-Volume Production
Servo Press:
The servo press integrates advanced servo motor technology to offer exceptional precision and flexibility in motion control. This makes it ideal for complex part production and applications where precise, customizable press movements are required.
Main Technical Parameters:
Nominal Force: 450-2000kN
Stroke Length: 4mm
Strokes per Minute: ~50-90min-1
Advantages:
High Precision
Flexible Stroke Control
Ideal for Complex Part Processing
Optional Features:
Real-Time Monitoring System
Customizable Motion Curves
Adaptive Pressure Control
Feeding type
Automatic Feeding System
This system includes various types of feeders, such as roller feeders, belt feeders, and others. It is designed to automatically load materials into the press for continuous production. The system supports a wide range of materials and ensures high feeding accuracy and speed.
Key Features:
Feeding Types: Roller Feeding, Belt Feeding, etc.
Material Range: [specific materials]
Feeding Accuracy: [specific value]
Feeding Speed: [specific value]
Advantages:
Increased Production Efficiency
Improved Processing Accuracy
Reduced Manual Handling and Labor Costs
Exchange Table System
The exchange table system allows for quick switching of workpieces, enabling one platform to be loaded while the other is in use. This system reduces downtime and improves production continuity.
Key Features:
Switch Time: [specific value]
Load Capacity: [specific value]
Dual-Platform Design
Advantages:
Seamless Transition Between Workpieces
Continuous Production Capability
Faster Loading/Unloading for Increased Efficiency
Other Feeding Methods
In addition to automatic feeding, manual feeding systems can also be used, especially for low-volume or customized production runs. Operators manually place materials into the press.
Key Features:
Suitable for Low-Volume Production
Simple Operation
More Flexibility for Small-Batch or Complex Parts
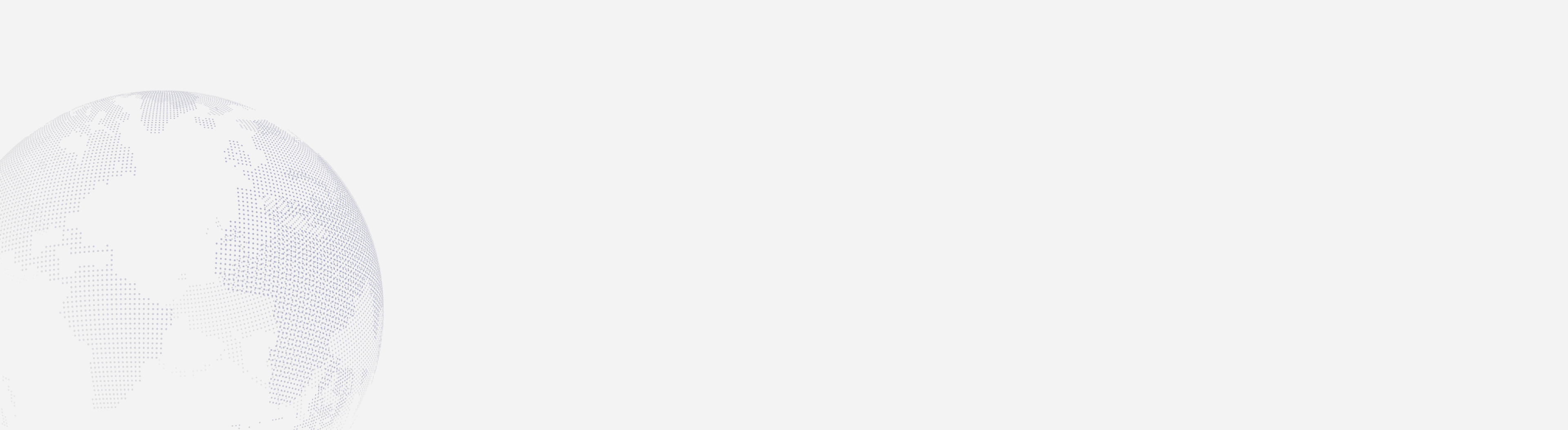